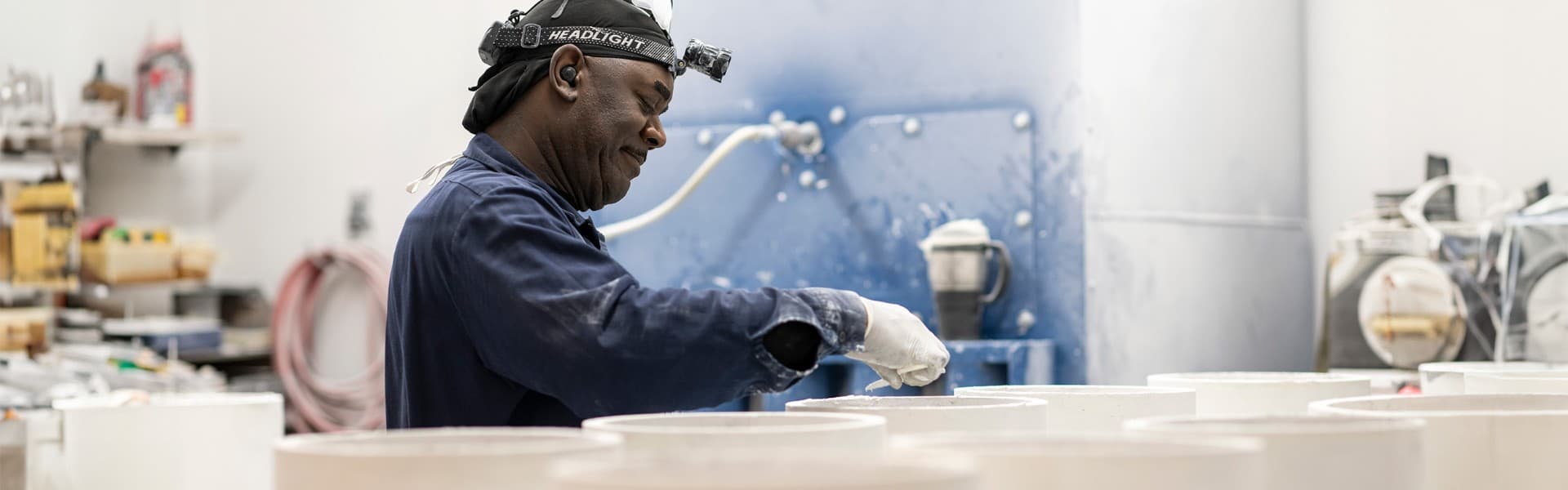
Manufacturing Processes
Our Processes
Offering An Array of Processes To Ensure Precision In Every Part We Make
With our extensive experience across diverse industries, we bring a wealth of knowledge and a commitment to delivering optimal performance for your operations. Our aim is to provide top-quality engineered parts, delivered as promptly as possible. Employing a range of techniques and materials, we cater to a broad spectrum of applications.
Bonding Systems
Oxide Bonded
Cement Bonded
Alumina Bonded
Nitride Bonded
Resin Bonded
Materials Used
Alumina
Alumina Chrome
Alumina Carbon
Alumina/Magnesia Spinel
Magnesia
Fused Silica
Oxide Bonded SIC
Nitride Bonded SIC
Alumina Bonded SIC
Alumina Zirconia Silica (AZS)
Within Our Facility, We Specialize In Four Major Processes
Patented Power Pressing
Utilizing the SXD process, our four machines produce high-density, uniformly shaped components with consistent performance characteristics. Our capabilities range from shapes weighing 10 to 5,000 lbs.
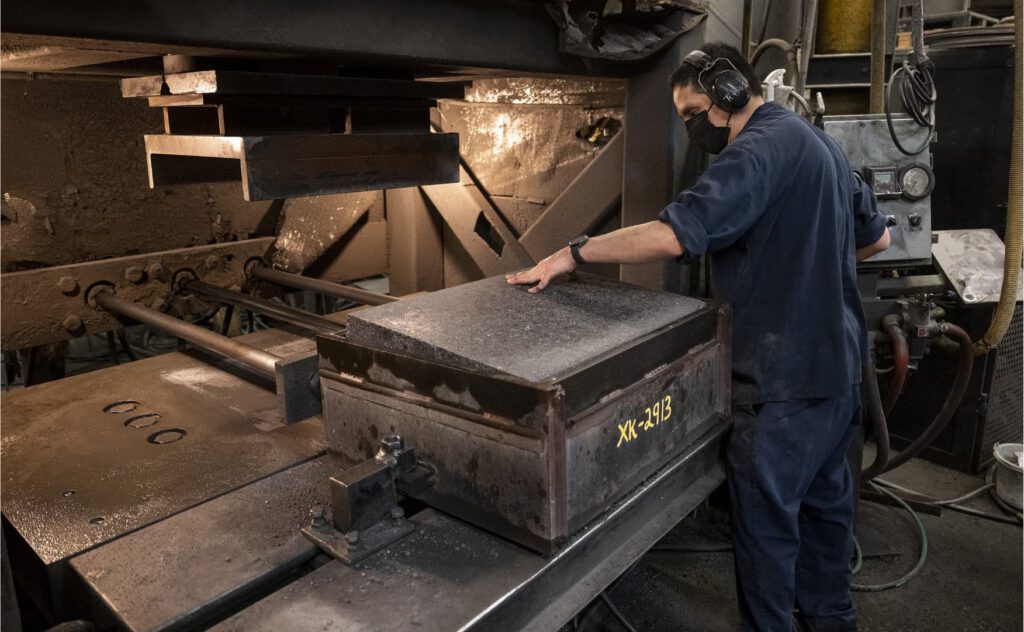
ISO-Tuff Injection
This proprietary technology allows us to produce net-shape ceramics with exceptional physical properties – ranging up to 3,000 pounds.
Unlike the traditional manufacturing processes, the ISO-Tuff process involves injecting the refractory mix under pressure, into precisely machined steel and/or aluminum or 3D printed molds. This process occurs within the ISO-Tuff injection chambers – technology that Holland developed over several years. Further process steps of bonding and solidifying the shape are the proprietary method that allows these shapes to achieve thermal shock resistant properties greater than that of any known competitive materials.
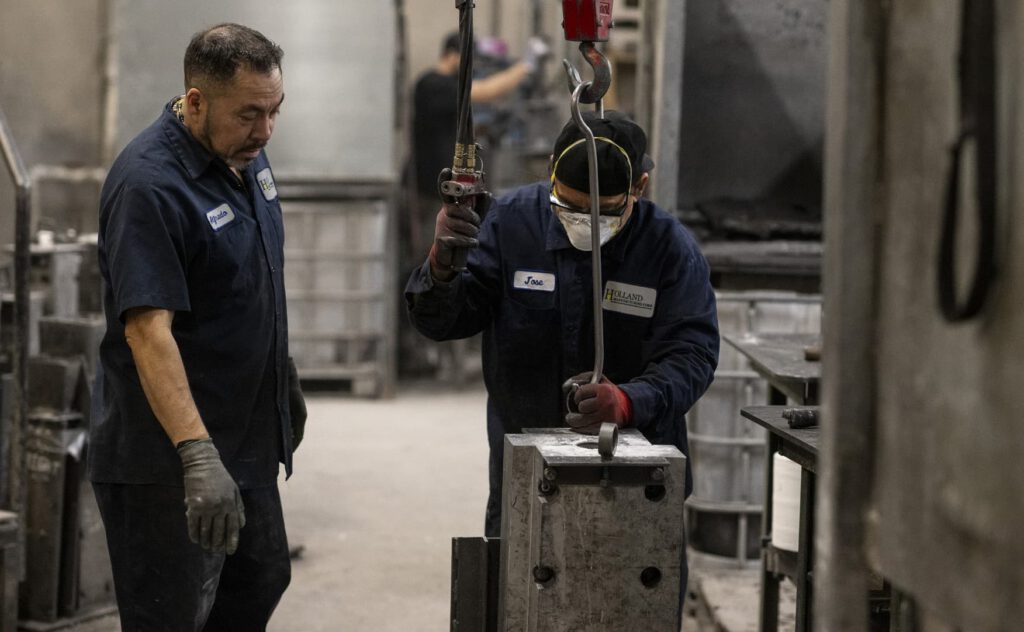
Casting
Our system incorporates both internally developed castables and those sourced from external suppliers, ensuring versatility and quality in our casting processes.
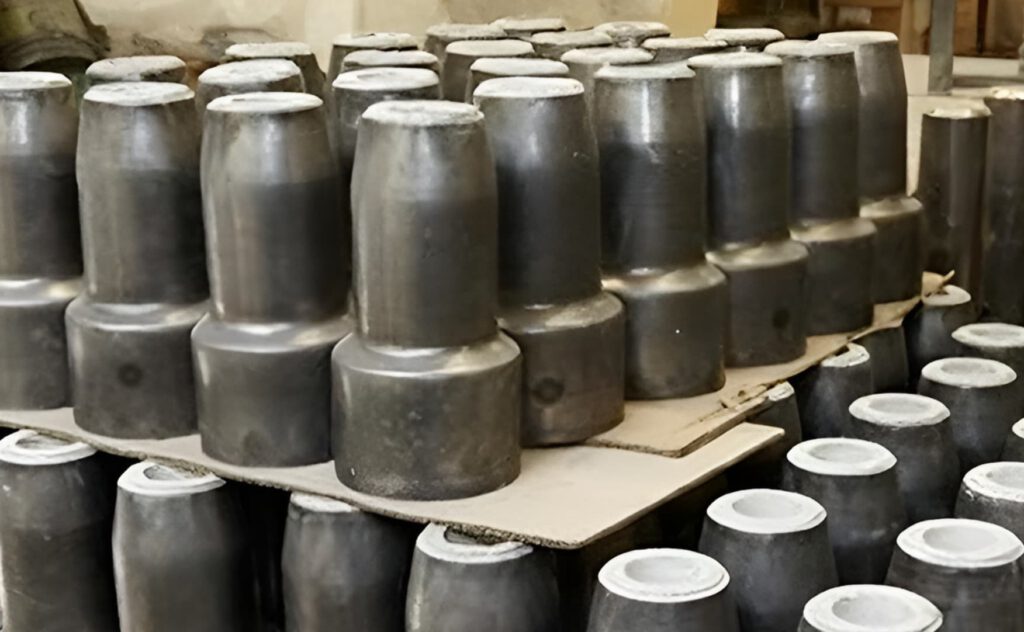
Post Manufacturing
Holland offers additional services such as saw cutting, drilling, and diamond grinding for refined finishing of fired ceramic shapes.
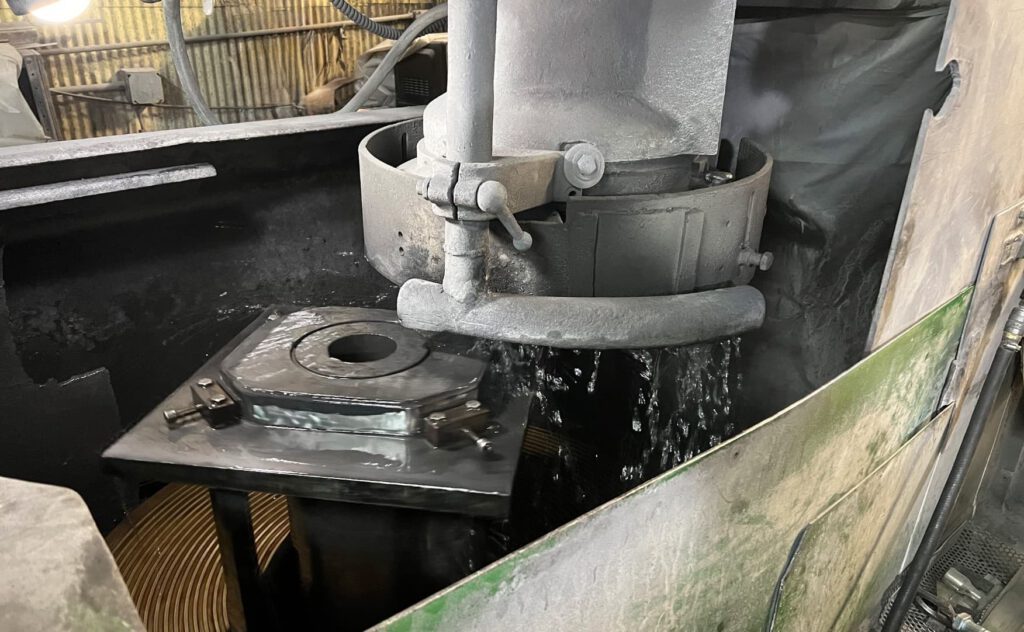