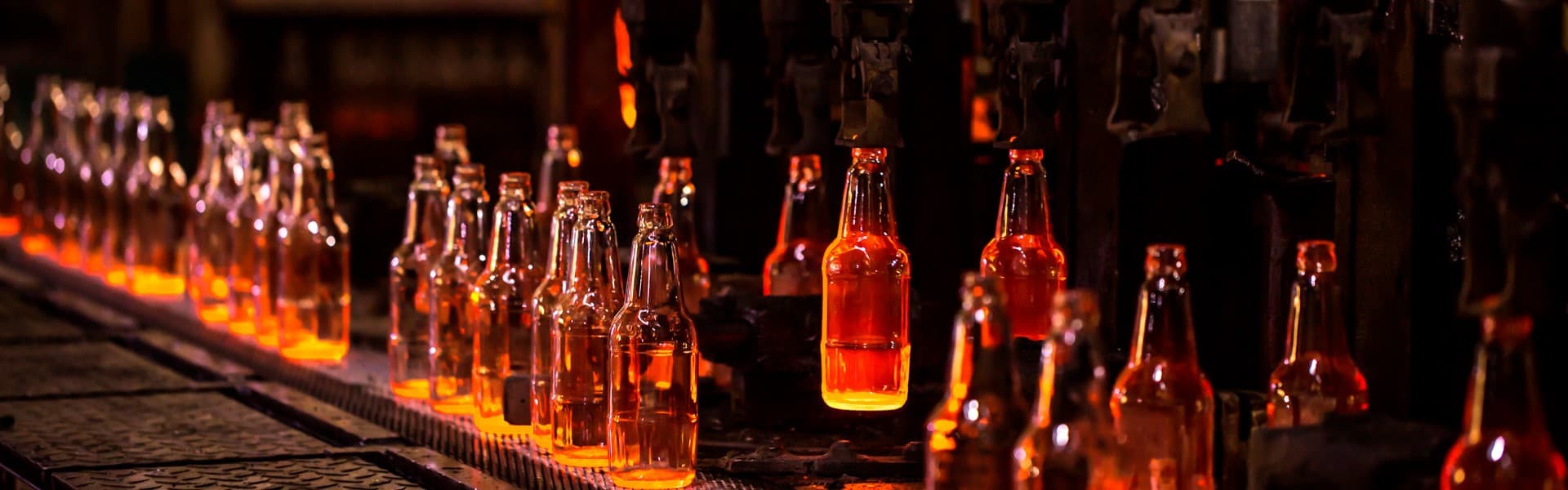
Glass Industry
Maximize Your Production Capabilities With Refractory Solutions Perfectly Tailored To Meet Your Unique Requirements
Glass Industry
Refractory shapes play a critical role in ensuring your glass operation operates at their highest possible efficiencies. By offering a wide array of experience and capabilities, we’re manufacturing high performing refractory shapes that are being installed in the melter, through the forehearth, to conditioning and forming areas.
With Holland, you’ll appreciate the remarkable lifespan of our refractory parts, offering longevity and reliability crucial for sustained productivity within your operation.
Feeder Parts – Enhanced Physical Properties
Our initial focus was on feeder refractory parts for gob forming machines used in the production of container and tableware glasses.
Customers immediately noticed a step-change improvement in feeder refractory performance – both in the way of increased life and sustained glass quality.
Thanks to the high density, low porosity, and enhanced uniformity of our material, Holland’s glass feeder parts routinely provide up to 2X the life of traditional cast refractory shapes. Additionally, refractory generated defects (seeds, blisters, and stones) are virtually non-existent – allowing the glass maker to pack more saleable glass in every box.
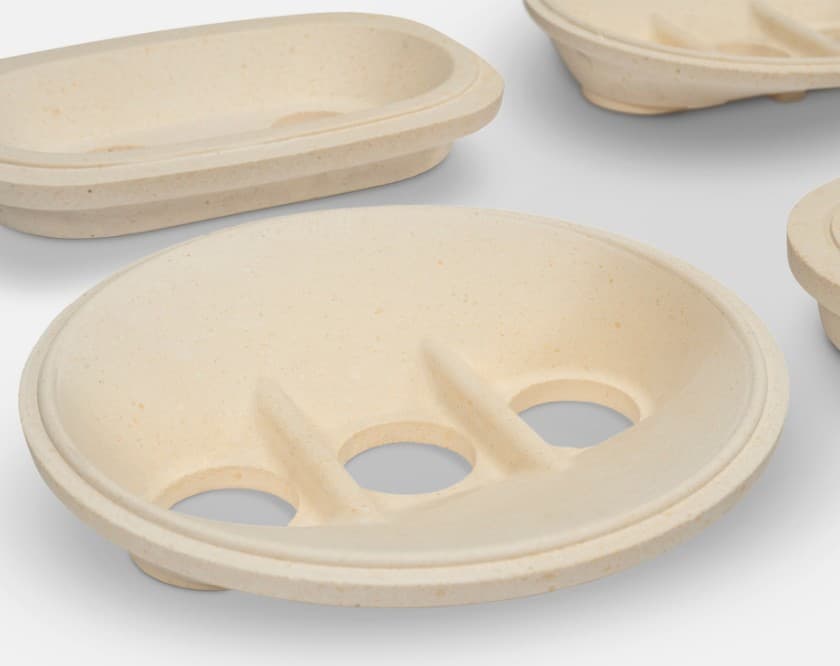
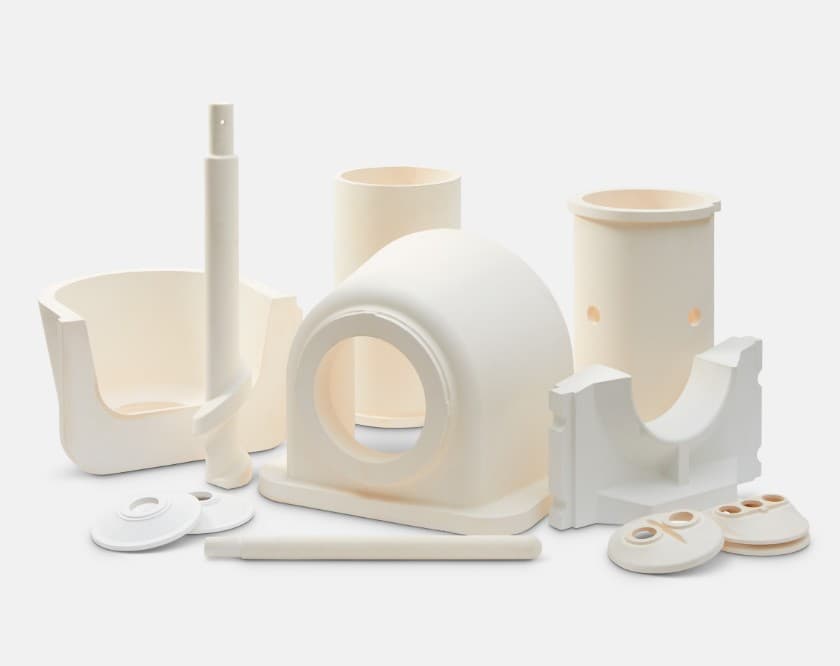
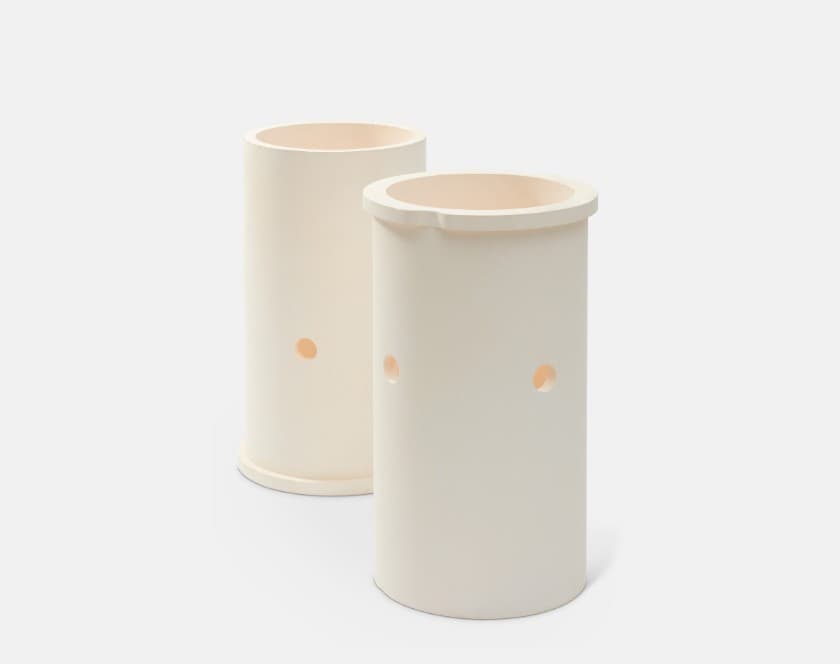
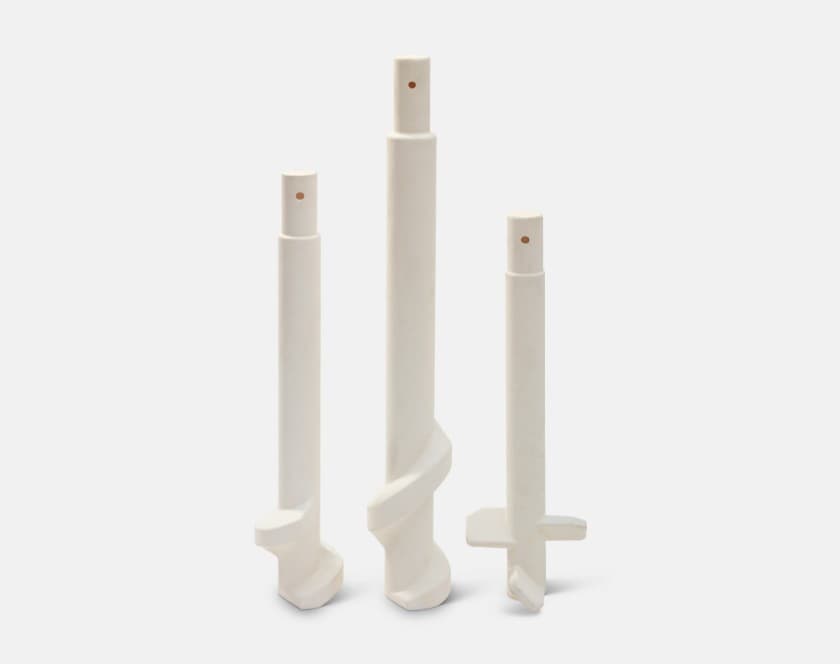
Shapes For Furnace, Refiner, Forehearth, Working End And Other Areas
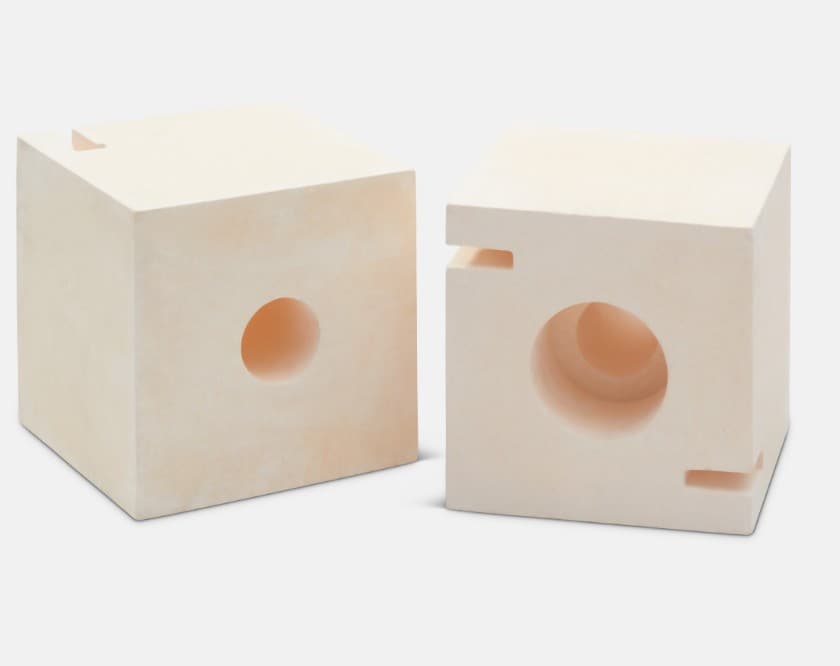
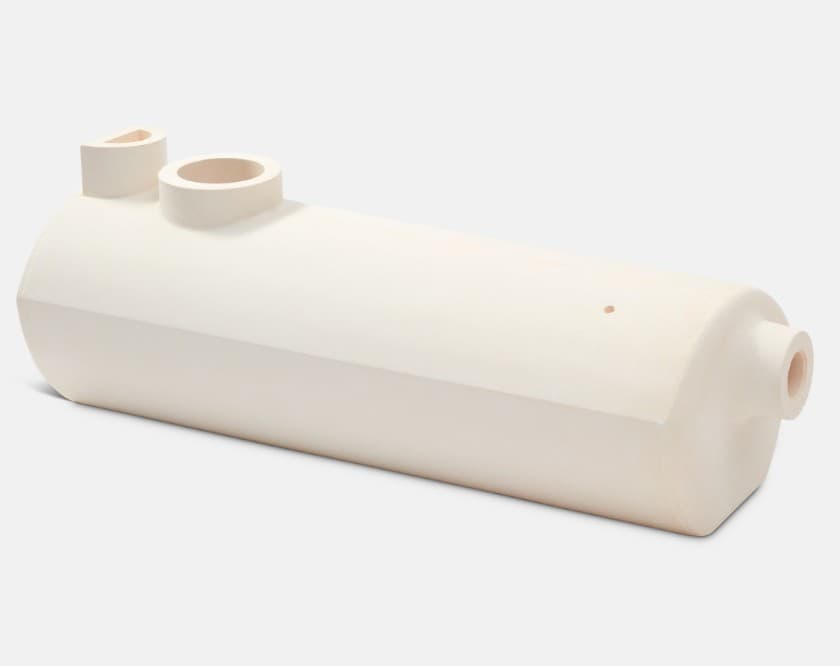
While our reputation for providing high quality feeder refractories spread throughout the industry, customers in all glass industry segments requested that we expand our supply of parts beyond just the gob forming machines.
Once we began providing shapes for the melting, refining and conditioning areas, glass companies immediately recognized a significant improvement in refractory operational performance – just as they had experienced with our feeder parts.
Our proprietary ISO-Tuff manufactured shapes became the most requested materials for use in these areas due to their excellent thermal-shock resistance, surpassing all previous market standards.
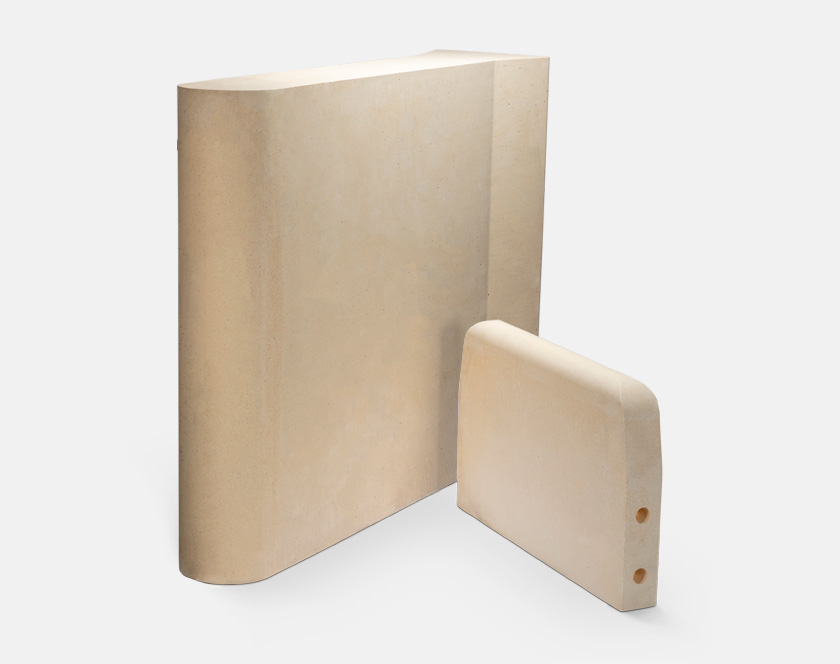
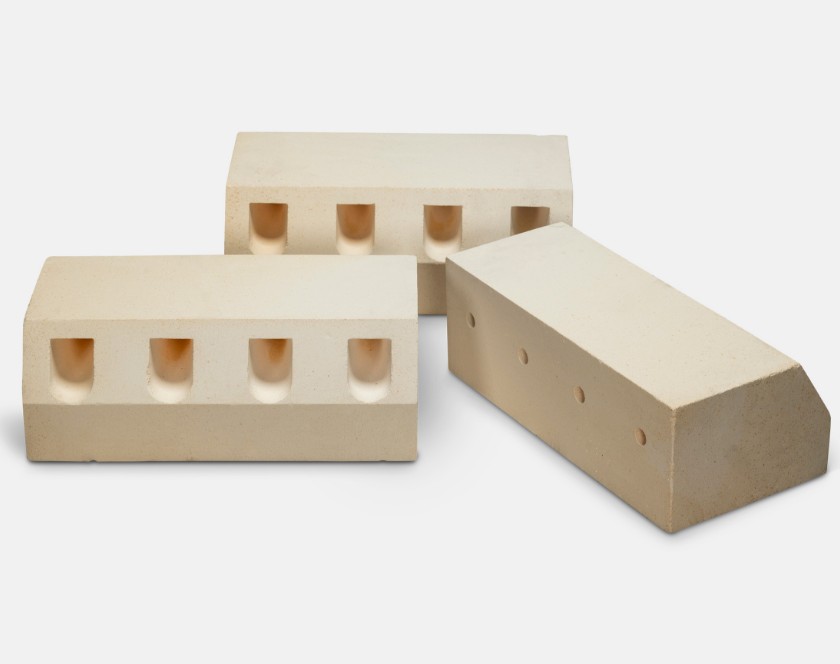
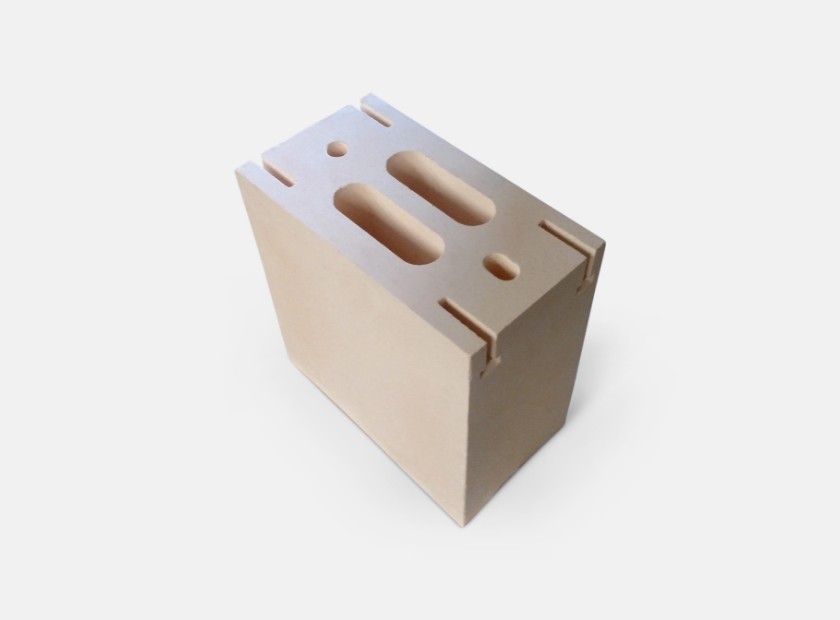
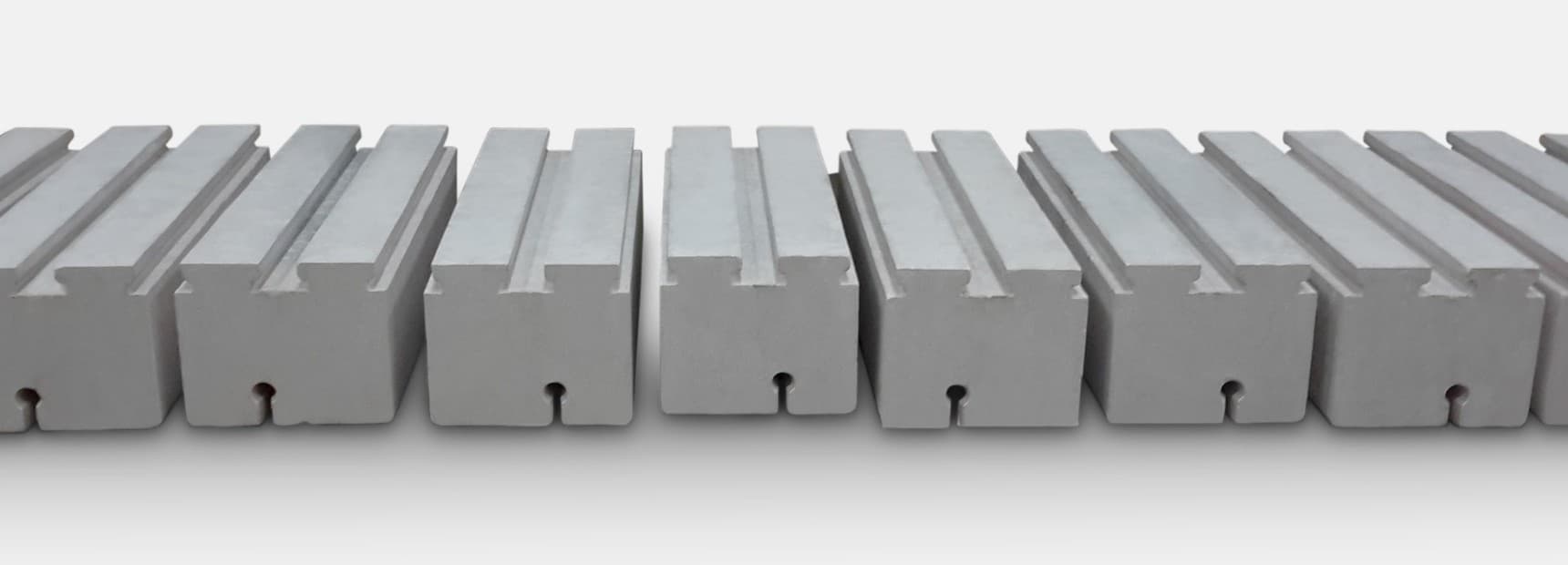
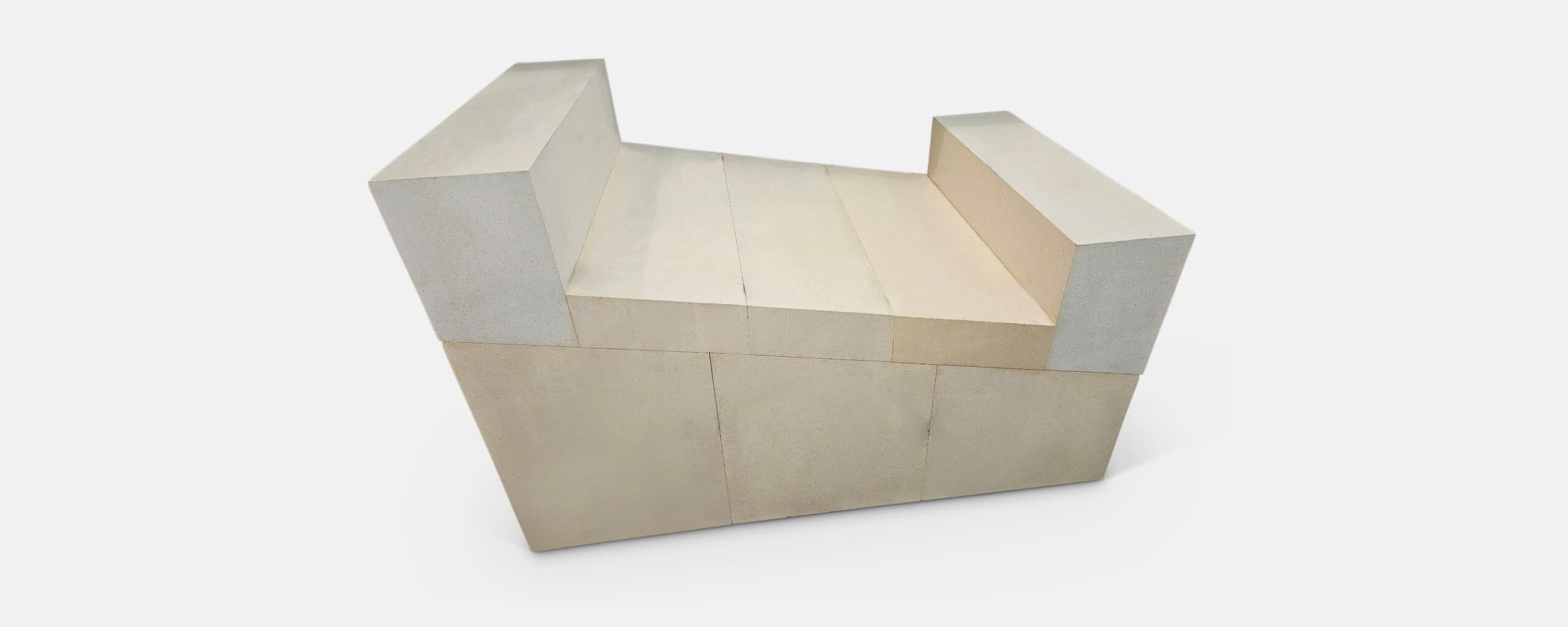
Select Refractory Shapes/Applications For All Segments of The Glass Manufacturing Industry
Float/Flat
Furnace Superstructure
- Burner Blocks
- Port Jambs and Damper Blocks
- Thermocouple Blocks
- Pressure Tap Blocks
- Furnace & Regenerator
- Peephole Blocks
- Waist Superstructure
- Working End Superstructure
Canal Superstructure
- Flat Arches
- Sealing Tile
- Dross Box Covers
- Spout Lip Support Tile
- Restrictor and Wetback Tile
Fiber
- Furnace Burner Blocks
- Peephole Blocks
- Bushing Blocks
- Forehearth Cover Blocks
Sodium-Silicate, Art & Specialty Glasses
- Burner Blocks
- Overcoat Tile
- Day Tank Assemblies
- Melting Crucibles
Tableware
Furnace Superstructures
- Burner blocks
- Peephole Blocks
- Doghouse Mantle Blocks
- Thermocouple Blocks
- Backwall, Breastwall, and Frontwall Blocks
- Feeder Expendables
Container
Furnace Superstructures
- Burner Blocks
- Peephole Blocks
- Doghouse Mantle Blocks
- Thermocouple Blocks
- Backwall, Breastwall, and Frontwall Blocks
- O2 Sensor Blocks
- Alcove, working end, refiner and forehearth – superstructure and substructure
- Throats – covers, sidewall, and facer blocks
- Melter Sidewall Blocks, Overcoats, and emergency hot repair shapes for both above and below glass
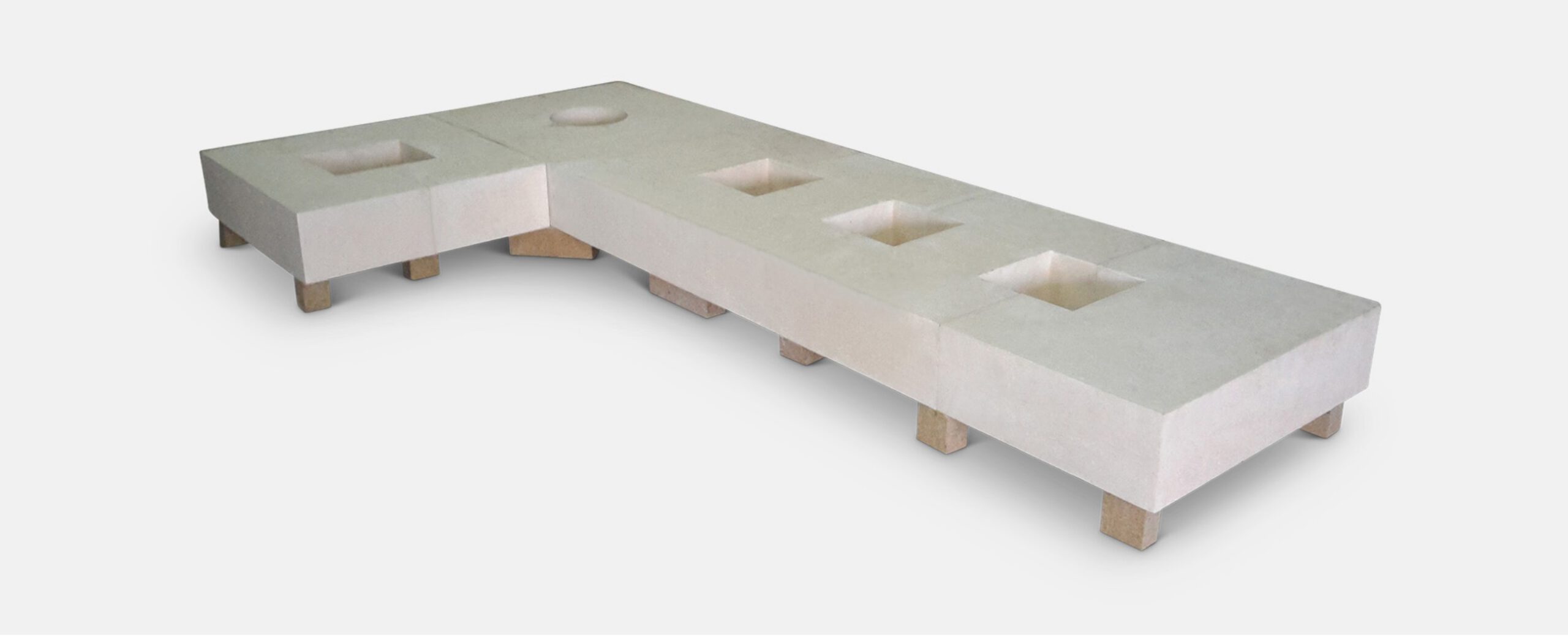